A new multi-function power supply unit for my Embedded Lab
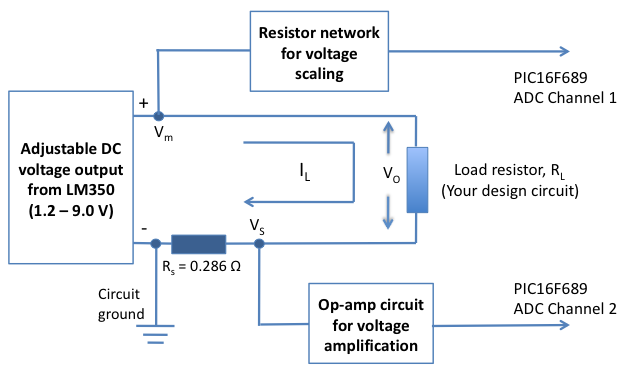
|
One important parameter in embedded system designing is power consumption. This parameter is directly related to the battery lifetime, if the system is to be powered from a battery. In order to determine the power rating of your designed system, you need to know how much current the system draws from the source at a given voltage. While working on my projects, I usually measure current by placing an external ammeter in series with the current’s return path. This is not always convenient to do, and so I thought of making a special power supply unit for my lab that would display both voltage and current information on a LCD screen while prototyping my circuit. This way I can continuously monitor how much power my test circuit is drawing at a specific operating voltage.
This power supply unit provides fixed ±5 V as well as a variable dc voltage ranging from 1.25 V to 9 V. A PIC16F689 microcontroller is embedded into the power supply unit to measure the adjustable output voltage along with the load current. Besides, this unit also has a built-in frequency counter to measure the frequency of an external signal. The range is over 50 MHz. However, it has been tested up to 20.0 MHz, and works fine. There are still few I/O ports of PIC16F689 that are not used. So I am thinking about adding one or more features (like capacitance meter) to it. But that would be on my second version.
Theory
The fixed ±5 V power supplies are derived using LM7805 and LM7905 regulator ICs. A 12 V rectified output from a center-tapped transformer provides the dc inputs to these regulator ICs. For the variable dc output, a LM350 IC is used. LM350 is an adjustable 3-terminal positive voltage regulator that is capable of supplying in excess of 3A over a 1.2V to 33V output range. It requires only 2 external resistors to set the output voltage. Since my dc input is only 12 V (rectified output from the transformer), the regulated output from the LM350 IC would go up to 9 V (3 V less than the input, as specified in the datasheet). In order to obtain the full range of output voltage (up to 33 V) from LM350, you need a transformer with a higher output voltage. I rarely use power supply above 5 V in my projects, and therefore, a variable voltage source up to 9 V is good enough for me.
Next comes PIC16F689 microcontroller that measures the LM350 output voltage and current. You are right, I am implementing voltage and current measurement only to the LM350 output. The principles of voltage and current measurements using microcontroller were discussed in two of my posts: PIC-based digital voltmeter and How to measure dc current with a microcontroller. I am not going to repeat the details here. Both the parameters can be measured with built-in ADC channels of PIC16F689. Since the output voltage from LM350 could go higher than 5 V (up to 9 V in this situation), it is not directly measurable from an ADC channel. A simple voltage divider network using two resistors is incorporated to scale down the output voltage to the safe ADC input range (0-5 V). On the other hand, the current to be measured must be first converted into voltage so that it could me measureable too with the ADC channels. The current to voltage conversion can be done by placing a small value resistance (shunt) in series with the current path. The voltage drop across the resistance will then vary linearly with the current. I am using a 0.286 ? resistor (Rs) made by myself by coiling a 5 ft long 22 AWG solid copper wire that has a plastic insulation on its outer surface (see the picture below).
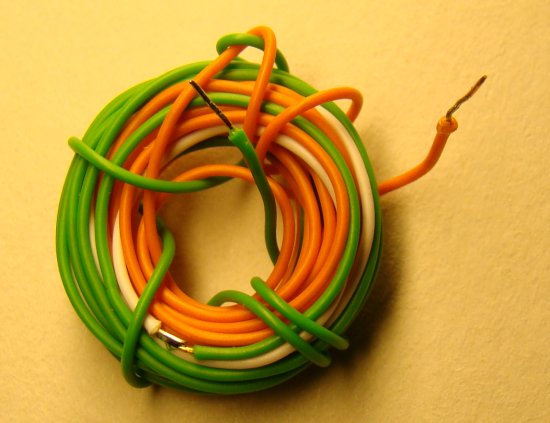
Current sensing resistor
Since this resistance is so small in value, the voltage drop across won’t be very high for small currents. Even for 1 A of current, the voltage drop across it would be only 0.286 V. To improve the resolution (and hence accuracy) of current measurement, this voltage must be amplified before the AD conversion process. An operational amplifier with a suitable gain can do this task. The figure below shows how this whole technique works.
An interesting thing to be noted here is that the output voltage across the load (Vo) is actually the measured voltage (Vm) minus the voltage drop across Rs (Vs). For small load current, the difference between Vm and Vo won’t be very much, but it could be significant for higher current. For 1 A of load current, the output voltage across the load is 0.286 V less than the measured output voltage from LM350. This error will be corrected later in the software part by subtracting Vs from Vm.
The frequency counter uses Timer0 module in counter mode to measure the frequency of an external signal. A single transistor preamplifier stage is used to boost the low amplitude signals before they are sent to the Timer0 module for counting. An easily available BF199 RF transistor is used for this purpose.
Circuit Diagram
As mentioned earlier, two linear regulator ICs (LM7805 and LM7905) are used to derive fixed ±5 V supply. A center-tapped transformer output is rectified (using diodes) and filtered (using 4700 µF capacitors) to obtain unregulated ±12 V dc that serve as inputs to both the regulator ICs. The circuit diagram below shows all the components and their connections required for the fixed power supply.
The variable power supply unit uses an adjustable regulator IC (LM350). The output voltage can be controlled through resistors R3 and Rp (see figure below). The expression for output voltage is, Vo ? 1.25 x (1+Rp/R3). This specific design allows the output voltage to vary from 1.25 to 9.0 V. R1 and R2 create a voltage divider network to scale the output voltage within the safe limit (0-5 V) of the microcontroller’s ADC channel. An additional zener diode at the output ensures that the input voltage at PIC’s ADC channel won’t be greater than 5.1 V. The scaled output is connected to AN0 channel (pin 19) of PIC16F689.
The measurement of current is possible with a shunt resistor (Rs = 0.286 ?) and an operational amplifier circuit. Rs is placed on the return path of the current and therefore, the voltage drop across it is proportional to the current drawn from the variable power source. This voltage is first amplified by a non-inverting Op-amp circuit and then passed through another non-innverting buffer stage to lower the output impedance. The output from the buffer goes to AN4 channel (pin 16) of PIC16F689 for A/D conversion. With R4 = 1.3 K and R5 = 12 K, the overall gain of Op-amp stage is 10.23. I am using LM324 IC for the Op-amp stage. LM324 does not provided rail-to-rail swing; the maximum output is about 1.5 V less than the applied power supply voltage. In this case, LM324 is powered with 0-5 V, and therefore, the maximum output voltage could be about 3.5 V. This means the maximum input voltage to the Op-amp stage would be 3.5/10.23 = 0.342 V. This gives the maximum range of the measurable current to be 0.324/0.286 = 1.2 A. Current values higher than this will saturate the LM324 output. The range of the measurable current can be increased either by decreasing the gain of the Op-amp stage or by using a different Op-amp IC that provides rail-to-rail output swing (0-5 V).
The preamplifier stage for the frequency counter has an RF transistor (BF199) that is collector-feedback biased using a 10 K resistor. The 1 K resistor with diodes D1 and D2 at the input side clamp the input signal levels to ±0.7 V. The 0.1 uF capacitor eliminates any dc component presented in the input signal. The amplified output is derived from the collector with a 470 ? resistor in series and is sent to T0CKI pin of PIC16F689. The Timer0 module counts the number of incoming pulses through the T0CKi pin to determine the incoming frequency.
PIC16F689 runs with an external 20.0 MHz crystal. A 16 x 2 character LCD (HD44780 compatible) is interfaced in 4-bit mode. Data were transferred through RB4-RB7 pins whereas the RS and E signals are controlled through RC7 and RC6 pins, respectively. A diode connected between RC1 and RA2 acts as a gating enable for frequency counter. When RC1 is high, the T0CKI input is also held high, disabling the counting process. RC1 is set to low when the microcontroller has to count the external pulses from the preamplifier stage output. The 470 ? resistor at the output of the preamplifier stage is to prevent any possible short circuit at T0CKI pin due to the voltage conflict between pins RC1 and RA2.
I constructed the complete circuit on a 180 mm x 128 mm general purpose prototyping circuit board which is shown below.
A/D Conversion Math
The use of A/D conversion for voltage and current measurements require some math to re-convert the digital outputs back to the voltage and current for display. Let’s work on displaying the voltage first. The analog input voltage (Va) at RA0/AN0 pin is related to the A/D conversion output (digital number, DN) as,
DN = Va * (1024/5) = 204.08 * Va (Vref = 5 V, ADC resolution is 10-bit)
or, Va = 0.0049 * DN
But Va = Vout * R2/(R1+R2), Vout is the actual output from LM350.
=> Va = 0.2418*Vout
=> Vout = 4.136 * Va = 4.136 * 0.0049 * DN
=> Vout = 0.0203 * DN
This is the conversion equation for calculating the LM350 output voltage from the 10-bit A/D conversion result (DN) for channel AN0.
Similarly, for current measurement, the output of Op-amp (V0) is related to the AN4 channel A/D output as,
V0 = 0.0049 * DN (just as above)
But V0 is related to the load current (IL) through Rs as,
V0 = 10.23 * IL * Rs = 10.23 * 0.286 * IL = 2.926 * IL = 0.0049 * DN
=> IL = 0.001675 * DN (gives current from A/D conversion output)
As mentioned earlier, the output voltage is actually less than the calculated voltage (Vout) under load condition. This is because of the voltage drop across the shunt resistor Rs = 0.286 ? due to current IL. The adjusted output voltage should be, therefore,
Vout = 0.0203 * DN – 0.286 x IL
Operation of Frequency Counter
The Timer0 module (no prescaler) is used as an external pulse counter whereas Timer1 module is used to generate a precise 100 ms duration as counting interval. This means that the resolution of frequency measurement is 10 Hz. This resolution is valid for frequencies up to 99990 Hz. Beyond this, the Timer0 module uses the prescaler (1:64) and the new resolution becomes 640 Hz or 0.64 KHz. As PIC16F689 is using 20 MHz clock, wit h 1:64 prescaler value, it can count frequencies over 50 MHz. The operation of frequency counter is like this.
- Initialize Timer1 registers with appropriate values for creating 100 ms delay.
- Enable Timer0 as counter with prescaler 1:64.
- Count the pulses for 100 ms.
- Frequency = 10 x No. of Pulses
- If frequency < 99990, change prescaler to 1:1, re-calculate frequency, and display it (in Hz). Otherwise, display the frequency in KHz.
Software
I used MikroC compiler to develop the firmware. The compiler has built-in library routines for A/D conversion, LCD display, and Timer operation. This makes the firmware development easier and quicker. Both the source code and HEX files can be downloaded from the link provided below. Configuration bits for PIC16F689 can be set using the project edit window in MikroC editor (shown below).
Download complete project source and compiled HEX files
Testing
The finished project is tested for voltage, current, and frequency measurement. The displayed voltage is cross-checked with an external voltmeter, and the readings are found consistent. A 56? resistor is connected as load to measure current. The output voltage is set to 5.2 V, and the displayed current is 90 mA. The ideal value of current should be 5.2/56 = 92.8 mA. This gives an error of about 3% in the measurement of current but the 56 ? resistor itself has tolerance of 5%. The testing frequency counter is done by applying the 20 MHz microcontroller clock derived from OSC2/CLKOUT pin (3). The displayed value is 20.00128 MHz which is really close.
|
I l just ran across this project while looking for something else and think this would make a great project.
Has anyone out there actually built one of these and did it function properly?
Please keep up the good work and Thanks….
F.W.
Pingback: USB Frekansmetre | elektrokod
sir may be am too late to ask this, im just a beginner of studying the PIC micro controller i have a doubt!
to measure the frequency, as measured I/P pin where the frequency measuring circuit starts,where the I/P pin should be connected first. or the circuit just starts from the beginining????????????
please help me to overcome this?
hope u got my question?
Hi! Can i use a 4700uf/16V instead of a 50V ?
thank you!
Marc
there is no change in current even when the current is below 1A and i even don’t see any current programming in the file
hey!! i am making this project. nice work by the way. can u pls help me by telling where to connect the load so as to get the voltage and current across it and displayed on the display.
It attracts visitors who are expected to become customers and to make purchases.
If you want to report spam employment advertisements to law enforcement,
you can contact the RCMP in Canada or the Internet Crime Complaint Center in the USA.
In the process, it would be wise to experiment which attacks
work and keep in mind that establishing a goof rapport with the people on your list must motivate them to buy anything from your products.
Dear RJ,
your embedded-lab is excellent
Thanks & regards
Bhavani Sankar Appalla,
UG Electronics lab,
IISc Bangalore.
u use the second stage of op-amp of current measurement as a buffer ???
is it important or i can remove it?
Hi Raj!
There’s no potentiometer for adjusting the voltage?
thanks!
marC:)
could you please state what D3 is from pin15 (RC1) to pin 17 (RA2) is on the diagram below where you wrote ..
A diode connected between RC1 and RA2 acts as a gating enable for frequency counter. When RC1 is high, the T0CKI input is also held high, disabling the counting process. RC1 is set to low when the microcontroller has to count the external pulses from the preamplifier stage output
I am very happy to know this site it’s really helpful to me,i am just a beginner to micro-controllers,and i really need help from professionals mean while i will like to know how i can set a adc value and set a particular port to be an output and secondly how to make a character to scroll on lcd screen i can make it to dispay but i dont know how to make it scroll…….
thanks
hello Sir
first of all i want to thank you for all the work you have done and sharing it with the world,I’m new in pic programing and i want 2 construct this project,i was able 2 buy all the components required
for this project except this one, pic16f689 i even tried ordering online from this website http://www.futurlec.com,sir is there any
pic i can use in place of this one? and is it possible to read voltage from 0v to 220v if its possible can you e-mail the source code and circuit to me,thanks very much for your time.
Hello,
Who can help me, i am a verry beginner with pic’s.
When i try to burn the pic with BubleBee, i become teh folowing message:
Verify error at adress 0x000000 value in image is 0x2D7A and value in target is 0x3700
Thanks.
want I resolution with 1Hz?. How do it?
Hi! i only have a 12 pins 120 VAC cord.. can i do with this?
thanks RAJ!
marC:)
I want to make this project for 1.2V to 24V DC output. can i use center taped transformer of 30Volt.
I want to make this project for 1.2V to 24V DC output. can i use center taped transformer of 30Volt. pl.reply on my email.
Thanks
Naresh Jethwa
bonjour. votre projet est très intéréssant . je suis débutant en pic et je voudrais utiliser votre projet avec uniquement la partie fréquencemètre et avec un pic 16F690. y a t-il un problème. salutations à vous lire.
Hi,
Sorry, you can delete that last comment. Found my mistake. I was connecting +5V instead of node ‘a’ to the 350. I’ll try and hold my questions for a few days next time so this doesn’t happen again 😛
Thanks 🙂
Hi again,
I’m testing my circuit right now on a solderless breadboard and have got the +/- 5V coming off the regulators, well 4.91V?/-5V. When I adjust the 5K pot my voltage output from the LM350 (LM350T) starts at around 1.25V as it should but then, before the pot is fully turned, it hits 4V and won’t go any higher (its supposed to go to 9V). I won’t rule out user error but it seems like something is saturating. I know its tough for u to help but do u have any ideas what might be happening? Thank you a ton!
@mister9,
What input voltage to the LM350 are you using?
Awesome thank you! I have a bunch of old VCRs!
Is that the parallel output voltage 12V @ 1A? When I go to order one off digikey I am asked if the transformer is Single Primary, Dual Primary, Quad Primary, Semi Toroidal, Single Secondary, Standard, Toroidal; and then a bunch of other stuff including information about the primary and secondary windings. Thank you again.
The one I have used is single primary, single secondary with center tap, 12V 1 A transformer. I didn’t buy it, actually I got it from an old VCR player’s power supply board.
A parts list would be nice.. I wrote all the parts down to get to do this as a side project but I’m confused what type of transformer to get as it is not mentioned. Could you help me with the specs of the transformer you used? Or perhaps a list of common electronics I might be able to salvage a transformer from for this. Thanks!
mister9,
You can select transformer based on your need. I am using a 12 V, 1 A transformer for it.
Hello Sir;
I wan t to know that of which circuit it gives the current ,means if i have separate circuit operated on 9 volt supply. and want to find out current through any resistance then how to find out with this instrument, is it possible ,if yes .How find it.
Please help me i m confuse in ammeter part, is this work like ammeter of our multimeter?.
Thank you!
hi please how can open all this files with what program?
@ sak,
These files are written for mikroC Pro for PIC compiler. The main project file has extension .mcppi. Open this in mikroC editor.
hello Sir,
i m very happy to see this its very fantastic …..fantastic side for embedded hobbies .i have read all article it is very clear and simple,which is not all other gives. some open their site to gain money.but your site is unique . it is god…… i have no word to say sir.
thanks for this side thank you very much .
You are welcome.
great project, very useful in system design, as I can see a diagram of the final.
Pingback: Multi-Function Bench Power Supply « Black Hat Security
great project.
you could create a single circuit schematic and put the project
in eagle design files
????? ???????
????? ???????
The way you have wired the LM350, the current sensing resistor will cause your output voltage to drop when you have higher current. You can solve this problem if you connect the lower end or the adjusting pot to the Vo minus.
The only drawback is that this way you add the current consumption of the regulator to the measured current. But since this is constant and small(1.25V/R3 = 1.7mA) you can easily correct for it in software or just ignore it.
This project is very similar to the kit sold by tuxgraphics.
Pingback: Multi-Function Bech Power Supply - Hack a Day
Pingback: Electronics-Lab.com Blog » Blog Archive » DIY Multi-function power supply unit